Stanton Elementary School
Washington, D.C.
Ryan DeJesso
Construction Management
Building Statistics
Building Name: Stanton Elementary School
Project Location: Washington, D.C.
Building Occupant Name: DC Scholars Stanton Elementary
Occupancy: Educational
Size: 83,700 sqft
Number of stories above grade: 3
Building Height: 50 ft
Primary Project Team
-
Owner: Department of General Services
-
Architect: Little Diversified Architectural Consulting
-
Structural Engineer: ReStl Designers, Inc.
-
MEP Engineer: Engenium Group
-
Civil Engineer: Wiles Mensch Corporation
-
Geotechnical Engineer: ECS
-
AV/IT/Security Consultant: Polysonics
-
Construction Manager/Estimator: Tompkins Builders
Dates of Construction: Building Completion – 12/28/2015
Site work Completion – 4/15/2016
Project Addition Cost: $16 million
Project delivery method: Design-Build with GMP
Architecture
Stanton Elementary School is a small 3-story building located in Washington, D.C. Following the addition that is currently under construction, the elementary school will increase in size from approximately 62,300 square feet to about 83,700 square feet. Once the renovation and addition have occurred, 46 classrooms will fill out the building’s floor plan.
A brick façade envelopes the front of the existing building. As a transition is made from the existing building to the building addition, the façade changes from brick veneer to a horizontal insulated metal panel facade. The building first floor addition that holds six classroom spaces utilizes a vertically aligned insulated metal panel façade. Additionally, a concrete masonry unit veneer is also used for the building façade in some instances.

3D model of the building design (Image Source: Tompkins Builders)
Codes and Zoning Regulations
Applicable Building Codes
-
2012 International Building Code
-
2012 International Existing Building Code
-
2012 International Energy Conservation Code
-
2013 District of Colombia Construction Code Supplement
-
2013 District of Colombia Green Construction Guide
-
2009 ICC/ANSI A117.1 Accessibility Code
-
Natural Fire Protection Association 101 2009
-
Natural Fire Protection Association 101 2012
Zoning Implications According to Washington, D.C. Zoning requirements
-
Green Area Ratio (GAR): 0.25
-
Maximum height allowed: 90 ft
-
Spires, towers, domes, pinnacles or minarets serving as architectural embellishments, penthouses over elevator shafts, ventilator shafts, antennas, chimneys, smokestacks, or fire sprinkler tanks may be erected to a height in excess of that which exceeds the maximum building height specified in the construction documents
-
If housing for mechanical equipment or a stairway or elevator penthouse is provided on the roof of a building or structure it shall be erected or enlarged as follows:
-
It shall be set back from all exterior walls a distance of at least equal to its height above the roof upon which it is located
-
-
Parking Spaces Requirements:
-
Elementary School: 2 for each 3 teachers and other employees
-
Parking Space Sizes: 9 feet x 19 feet
-
Building Enclosure
While the existing building features a brick veneer façade, the building addition displays more of a contrast in materials by using a variety of curtain wall facades including a horizontal insulated metal panel façade, a vertical insulated metal façade, and a long glass curtain wall at the building’s parking lot entrance. The metal panel curtain walls are fastened directly to the structural steel.
Roofing design utilizes a composite roof deck with a 2-inch metal deck topped with 4 inches of normal weight concrete. Green roof design requires the following elements:
-
Waterproofing layer
-
Insulation
-
Root barrier
-
Drainage layer and interior draining system
-
Filter fabric
-
Media

Metal Curtain Wall Detail. (Image Source: Tompkins Builders)
Sustainability
The project is aiming to obtain a LEED Silver certification in compliance with the LEED 2009 for Schools, New Construction, and Major Renovations guidelines. Based on LEED goals identified by the LEED project checklist, the building is currently on pace to receive 62 out of 110 possible points which would make Stanton Elementary School a LEED Gold certified building. Sustainable construction methods for innovation and design process are a large focus in gaining LEED points throughout the project. Additionally, recycling project materials and using more energy efficient systems will occur throughout the course of the project to earn LEED points and make for a more sustainable project. The building green roof plays a role in the focus on sustainability that is seen throughout this project. The green roof is present on the roof of the building addition and is depicted in the figure below.
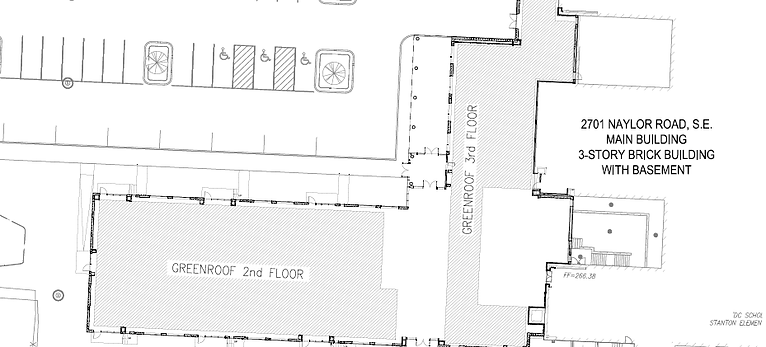
Green Roof Plan for Building Addition (Image Source: Tompkins Builders)
Structural System
The building utilizes a steel superstructure with mostly bolted connections. The floor system is a composite deck that is composed of four inches of lightweight concrete on top of a two inch 20 gage deck. In the pre-kindergarten wing, beam sizes range from W8x15 to 21x50. Typical girders are W24x68. In the remainder of the building, beam sizes range from W8x15 to W16x26. Typical girders throughout the remainder of the building are between W24x62 and W27x94. Column sizes range from W10x33 toW10x77 throughout the structure.
The building superstructure is supported by a building foundation that features a pile and pile cap system and a continuous footing system. The pile and pile cap system uses a total of 262 helical piles that are capped by a variety of eleven differently sized pile caps. Helical piles range from depths of 5 to 30 feet from the base of its respective pile cap. Variability in soil bearing capacity throughout the site calls for the large difference in drilling depth. The continuous footings run along the perimeter of the building. The foundation wall is concrete masonry unit wall.
Electrical System
The electrical system power is provided to the main switchboard MDPH. Switchboard MDPH supplies power to distribution panels MPDL and GEN. Switchboard MDPH also supports mechanical roof top units, condensing units, kitchen loads, standby loads, and lighting in the building addition. This switchboard operates as a 265 V/460 V system. Distribution Panel MDPL supports the power risers, building addition power, basement power, the HVAC riser, mechanical room loads, and stage lighting. This switchboard operates as a 120 V/ 208 V system. Distribution Panel GEN supports the fire pump, life safety lighting, the building addition elevator, and standby power. This switchboard operates as a 277 V / 408 V system.
Lighting System
The building lighting is defined by seven major unique zones: classrooms; corridors, lobbies, and vestibules; cafeteria; multipurpose room; private offices and open offices; conference rooms; and stairwells. Classroom lighting uses dimmable ballasts and is broken into three different zones that separate the front of the room, the middle of the room and the back of the room. Lighting for the building’s corridors, lobbies, and vestibules are controlled by a time clock in a centralized lighting control system. A low voltage override switch is used to turn on the lights in these areas during after-operation hours. The cafeteria uses a simple low voltage two-button switch at each entrance.
The multipurpose room has the most involved lighting system, for it includes lighting for the stage within this space. At the room’s entrances, the lighting system is operated by a low voltage two-button switch. A five-button switch is located behind the stage and used for stage lighting specific to scene control. All light fixtures are equipped with dimmable drivers/ballasts between 10% and 100% light output. Each row of fixtures moving back on the stage is under a separate zone.
Office spaces utilize a low voltage two button system. Both the office spaces and conference room spaces use dimmable ballasts. The building stairwells use dimmable ballasts as well. The building stairwell lighting is unique based on the fact that it is tied into the life safety power panel. The classrooms, cafeteria space, offices, conference rooms, and stairwells all utilize occupancy sensors that trigger the lighting within those spaces to emit light up to 100 percent output as an individual enters that space.
Mechanical System
The mechanical system was designed based on a 91-degree Fahrenheit summer dry bulb temperature in the summer and an 11-degree Fahrenheit winter dry bulb temperature. The mechanical system used in the school is a variable refrigerant flow system using variable air volume terminals for distribution. The air temperature and output is controlled by a building automation system computer. This automation system is interconnected between the rooftop mechanical equipment, variable refrigerant flow condenser units, and variable air volume output terminals to regulate desirable building temperatures. This system is supported mostly by switchboard MPDH. Mechanical rooftop and condensing units receive power from the main switchboard MDPH. The mechanical riser and smaller mechanical equipment spread throughout the building receive power from distribution panel MDPL.
Fire Protection System
Fire protection within the building occurs with a quick response sprinkler system with a 155-degree Fahrenheit rating. Sprinkler heads are semi-recessed in the ceiling except for in the main lobby where sprinkler heads are recessed with a cover plate. All sprinklers within the building cover an area of 1500 square feet. Most sprinklers within the building release at a water pressure of 0.15 gallons per minute per square foot area. Fire protection main piping is 2.5” and larger. Branch piping is 2” inches and smaller. The building standpipe in stair A is a 6” pipe. Stair T uses a 4” standpipe.
The fire alarm system includes fire alarm strobe lights in each room, whether the room is a classroom, office, or corridor. Classrooms feature extra protection, as they each have fire alarms in addition to the strobe lights, and a fire alarm manual station. Bathrooms also have a fire alarm and strobe light combination. Smoke detectors are located on each floor in the elevator lobby. The fire alarm system is tied in with various building systems to limit the spread of smoke during a fire. The system is able to shut down mechanical units, activate the alarm indicator system, recall the elevator to the primary floor, and close dampers in the mechanical units.
Construction Methods
Key elements of building construction include demolition of the existing building, the helical pile and pile cap foundations, erection of the structural steel, placement of the glass curtain wall at the building’s back entrance, and the installation of the green roof atop both sections of the building addition. The biggest issue with construction was the installation of the helical piles. This system was not originally in the scope of work, for the original design called for spread footings as the building’s main foundation. This was changed due to inconsistent soil conditions during excavation and the lack of confidence that the soil bearing capacity would be enough to support the weight of the large spread footings. Technical Assignment 3 covers a lot of the key methods along with issues and concerns of construction of major building systems.